Understanding Tooling Mold: A Comprehensive Guide for Metal Fabricators
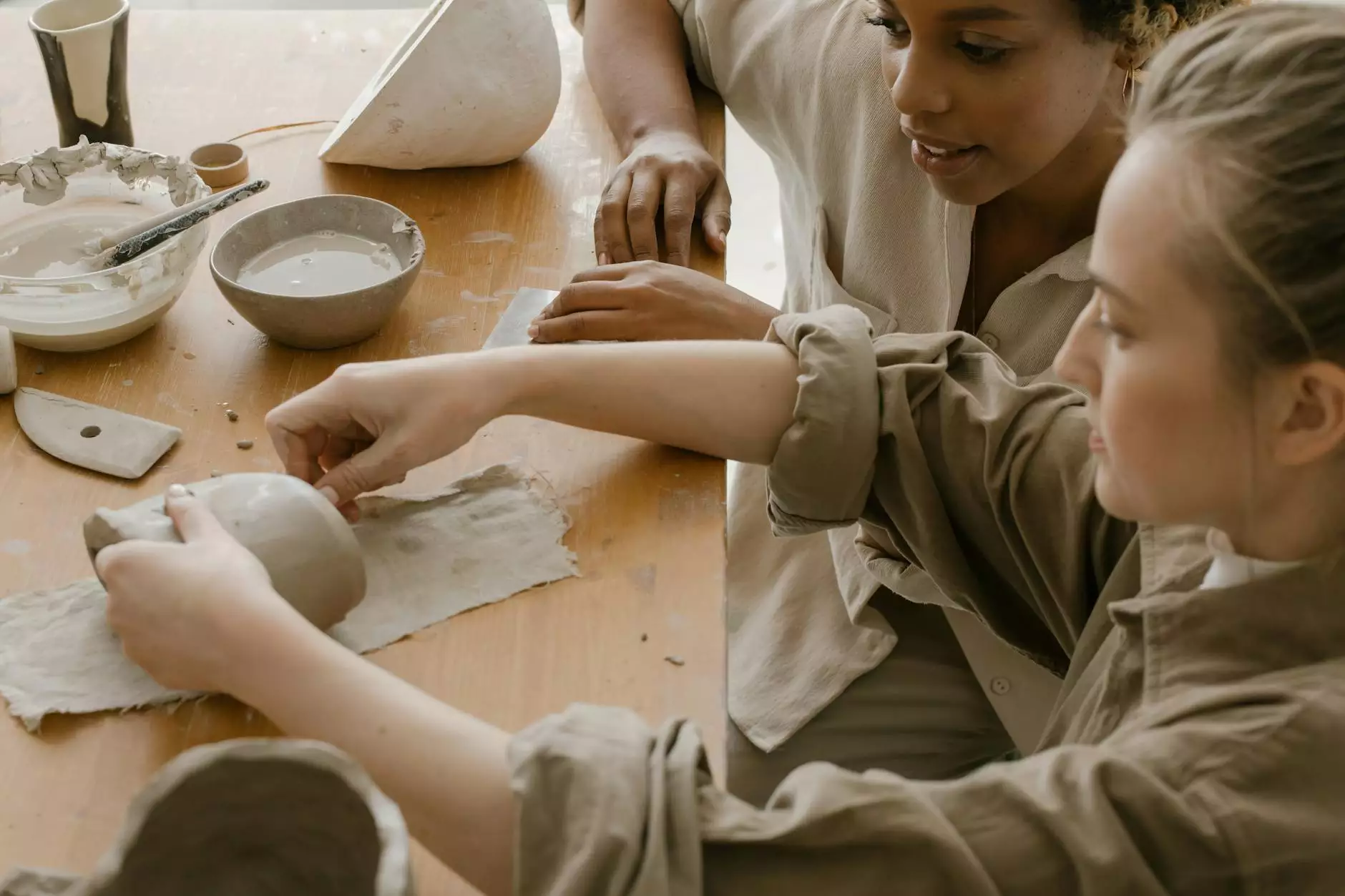
In the world of manufacturing and metal fabrication, the terminology can often be overwhelming. However, understanding key concepts like tooling mold is crucial for maximizing efficiency and quality in production processes. This article will delve deeply into what tooling molds are, their types, applications, and the profound impact they have on productivity in the realm of metal fabrication.
What is a Tooling Mold?
A tooling mold is a crucial component in the manufacturing process, often used in the creation of parts and products. Essentially, a mold acts as a template that shapes materials into the desired form. In metal fabrication, tooling molds play a pivotal role in producing complex components with precision.
The Importance of Tooling Molds in Metal Fabrication
When it comes to metal fabrication, tooling molds serve several essential functions:
- Precision and Accuracy: Molds ensure that each part is produced to exact specifications, reducing waste and improving quality.
- Efficiency: By using molds, manufacturers can produce large quantities of identical parts in a shorter timeframe, streamlining the production process.
- Cost-Effectiveness: Investing in high-quality tooling molds can significantly lower production costs over time by minimizing errors and waste.
Types of Tooling Molds
There are several types of tooling molds, each suited to different manufacturing needs. Understanding these types can help metal fabricators choose the right mold for their specific projects:
1. Injection Molds
Injection molds are widely used to produce parts by injecting molten material into the mold cavity. This method is ideal for complex shapes and is commonly used in plastic and metal fabrication. The benefits of injection molding include:
- High production rates.
- Ability to create intricate designs.
- Consistent quality across produced parts.
2. Blow Molds
Blow molds are employed primarily for shaping hollow parts. This technique involves inflating a heated plastic tube within a mold to form the desired shape. Key advantages include:
- Cost-effective for large production runs.
- Minimized waste of material.
- Ability to produce complex geometries.
3. Compression Molds
Compression molds are used for shaping materials under heat and pressure. This process is commonly applied in the production of rubber and thermosetting plastics. Key characteristics include:
- Simplicity in design.
- Flexibility for various material types.
- Low initial tooling costs.
Applications of Tooling Molds
Tooling molds are used across a wide array of industries, showcasing their versatility. Here are some common applications:
1. Automotive Industry
The automotive industry relies heavily on tooling molds for manufacturing various components, including dashboards, body panels, andengine parts. The use of precise molds is vital for ensuring the safety and performance of vehicles.
2. Consumer Products
From electronics to household goods, many consumer products are designed and produced using tooling molds. This ensures each product meets quality standards and performs reliably for the consumer.
3. Aerospace and Defense
In the aerospace sector, the use of high-quality tooling molds is critical for producing parts that are lightweight yet durable, ensuring compliance with strict safety regulations.
Choosing the Right Tooling Mold for Your Needs
Choosing the correct tooling mold for your project involves considering several factors:
- Material: Different materials may require different types of molds.
- Volume: High production volumes may justify investing in more complex molds.
- Complexity: Assess the intricacy of the design and select a mold that can handle those specifications.
Benefits of Investing in Quality Tooling Molds
Investing in high-quality tooling molds can pay off tremendously in the long run. Here are several benefits to consider:
- Durability: Quality molds last longer, reducing the need for frequent replacements.
- Operational Efficiency: Improved mold performance leads to smoother operations and less downtime.
- Enhanced Output Quality: High-quality molds produce parts with better finishes and tighter tolerances.
Innovations in Tooling Mold Technology
The field of tooling molds is constantly evolving, thanks to advancements in technology. Some notable trends include:
- 3D Printing: The use of 3D printing technology allows for rapid prototyping of molds and components, drastically reducing lead times.
- Smart Molding: Integration of IoT and AI in molding processes helps monitor performance and predict maintenance needs, enhancing efficiency.
- Biodegradable Molds: As sustainability becomes a priority, manufacturers are exploring biodegradable materials for molds, pushing the boundaries of traditional metal fabrication.
Best Practices for Maintaining Tooling Molds
To ensure the longevity and effectiveness of your tooling molds, consider implementing these best practices:
- Regular Cleaning: Mold maintenance begins with keeping them clean to avoid contamination and defects in the produced parts.
- Inspecting for Wear: Regularly check molds for signs of wear and damage to address issues promptly.
- Proper Storage: Store molds in a climate-controlled environment to prevent warping or damage.
Conclusion
In the competitive landscape of metal fabrication, understanding the role and importance of tooling molds can significantly enhance a company's operational efficiency and product quality. By recognizing the diverse types of molds, their applications, and the technology behind them, businesses can make informed decisions that lead to excellence in manufacturing.
Investing time and resources into selecting and maintaining quality tooling molds is not just a matter of convenience; it is a crucial step toward long-term success in the manufacturing industry. As you move forward, keep these insights in mind and consider how high-quality tooling molds can transform your production process for the better.