Understanding 160i: A Comprehensive Guide to Cutting and Welding Equipment
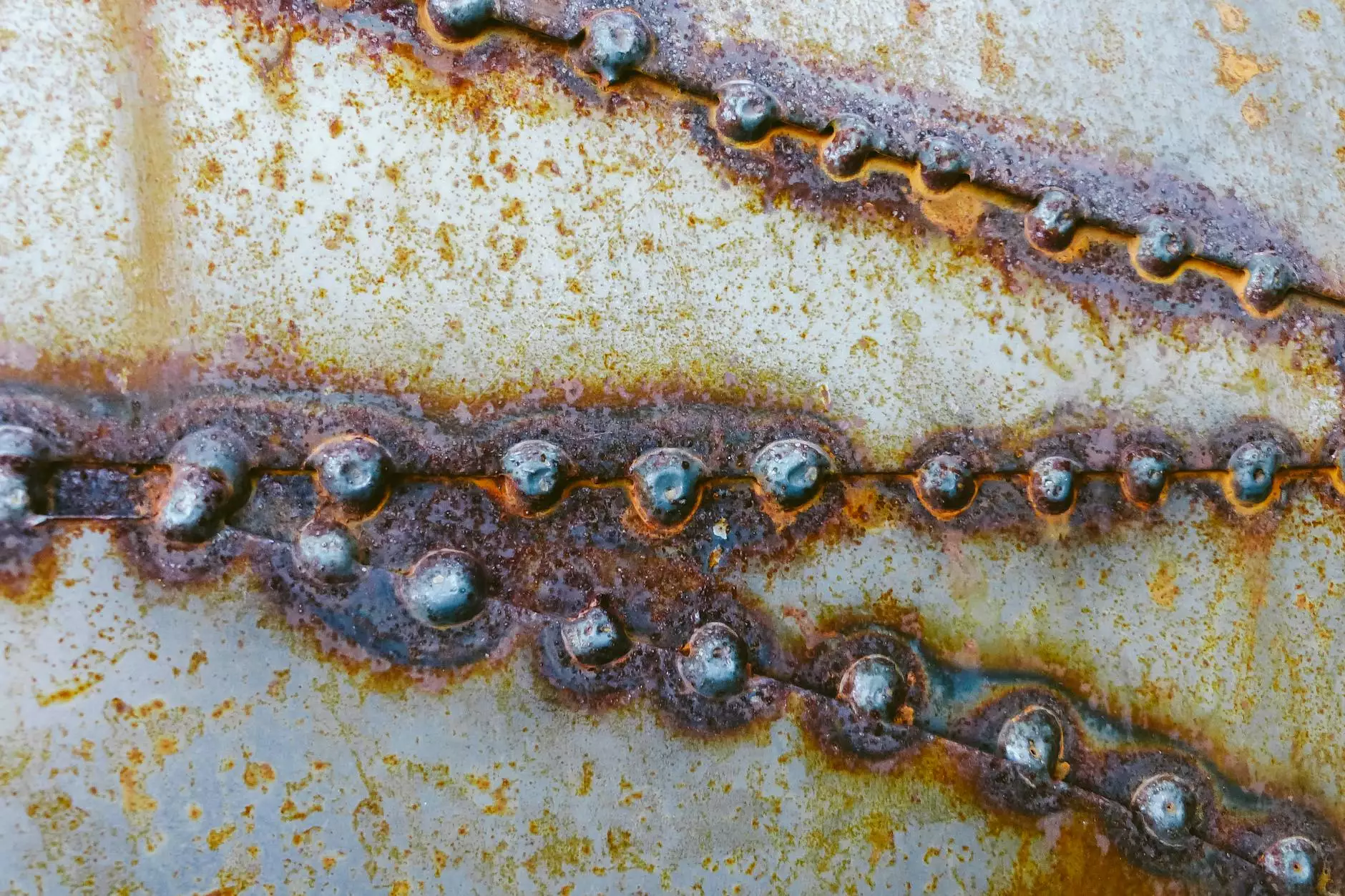
In the ever-evolving world ofcutting and welding equipment, understanding the terminology and various specifications is crucial for professionals and hobbyists alike. One term that frequently comes up is "160i." This article will delve deep into what 160i signifies, its applications, and how it fits into the broader category of cutting and welding equipment. Our goal is to provide you with a comprehensive resource that will help you make informed decisions in your projects and operations.
What is 160i?
The designation 160i typically refers to a type of inverter welding machine, specifically designed to operate at 160 amps. The "i" stands for inverter technology, which allows for precise control and efficiency during the welding process. The primary advantage of inverter welders is their ability to provide consistent performance, reduced power consumption, and lightweight portability, making them ideal for various cutting and welding applications.
Why Choose 160i Welding Equipment?
When considering welding equipment, one must evaluate the specific needs of the projects at hand. Here are some of the primary reasons why choosing a 160i inverter welding machine could be beneficial:
- Efficiency: Inverter technology translates to better energy conservation. The 160i units typically consume less power compared to traditional welding machines, leading to lower electricity bills.
- Portability: Due to their compact design, 160i welders are lightweight and easy to transport, making them perfect for on-site work.
- Versatility: These machines can perform a variety of welding processes, including MIG, TIG, and stick welding, depending on the configuration.
- Precision: The ability to control the current output allows for greater precision in welding, useful when working with delicate materials.
The Mechanics of the 160i Welding Machine
160i machines use high-frequency inverter technology which allows for significant advancements in the welding process. Here’s how they work:
- Rectification: The first step involves converting AC power from the mains supply into DC power.
- Inversion: This DC power is then switched at high frequencies using transistors, creating a more manageable and stable output.
- Transformation: The high-frequency current is transformed back to a lower frequency output suitable for welding.
- Feedback Control: Advanced feedback systems continuously monitor the output, ensuring consistent performance.
Applications of the 160i Equipment
The 160i inverter welding machine finds its place across various sectors, including but not limited to:
- Metal Fabrication: Ideal for both light and heavy metal fabrication due to its adjustable settings.
- Automotive Repair: The precision and control offered by 160i welders make them suitable for automotive applications.
- Construction: Used in building frameworks, gates, and other structural elements.
- Art & Sculpture: Artists and sculptors utilize these machines for intricate metal works.
Key Features of 160i Welding Machines
Investing in a 160i welding machine offers numerous features that enhance its usability and performance. Here are some essential features to look for:
- Adjustable Amperage: The ability to adjust the amperage from 10A to 160A, allows for versatility across various welding tasks.
- Overload Protection: Ensures that the machine does not overheat or get damaged due to high usage.
- Hot Start: A function that helps start the arc easier, specifically beneficial for electrode welding.
- Anti-Stick Technology: Prevents the electrode from sticking to the workpiece, enhancing performance and safety.
Comparing 160i to Other Welding Machines
While there are various types of welding machines available, 160i stands out due to its unique features and benefits. Let’s compare it briefly with some other options:
160A Stick Welders
Stick welders are typically more robust and less expensive, but they lack the precision of an inverter machine. If you need versatility and efficiency, 160i is the better choice.
MIG Welders
MIG welders are excellent for continuous welding, and while they may offer similar amperage, the 160i inverter machine provides better control and can handle a wider variety of welding techniques.
TIG Welders
TIG welders are typically more advanced and can accomplish intricate tasks; however, they are generally more expensive. For most entry-level applications, a 160i welding inverter may be more practical.
Safety Considerations When Using 160i Welders
While 160i welders are user-friendly, safety should always be prioritized when operating any welding equipment. Here are some key safety measures:
- Personal Protective Equipment (PPE): Always wear the appropriate PPE such as helmets, gloves, and protective clothing.
- Work Area Safety: Ensure that your work area is free from flammable materials and has adequate ventilation.
- Electrical Safety: Check all cables and connections before use to prevent electrical shocks and short circuits.
- Training: Ensure that all operators are trained and familiar with the machine's functionalities and safety protocols.
Conclusion: Embrace the Power of 160i in Your Operations
The 160i inverter welding machine represents an excellent investment for anyone serious about cutting and welding tasks. With its advanced technology, efficiency, and versatility, it allows for a wide range of applications while ensuring high-quality results. Whatever your project may be, embracing the capabilities of a 160i welder can substantially enhance your productivity and output.
Visit tiendaguve.com to explore a wide range of cutting and welding equipment including the 160i units, and discover how you can optimize your operations today!