Understanding Die Casting Parts Manufacturers
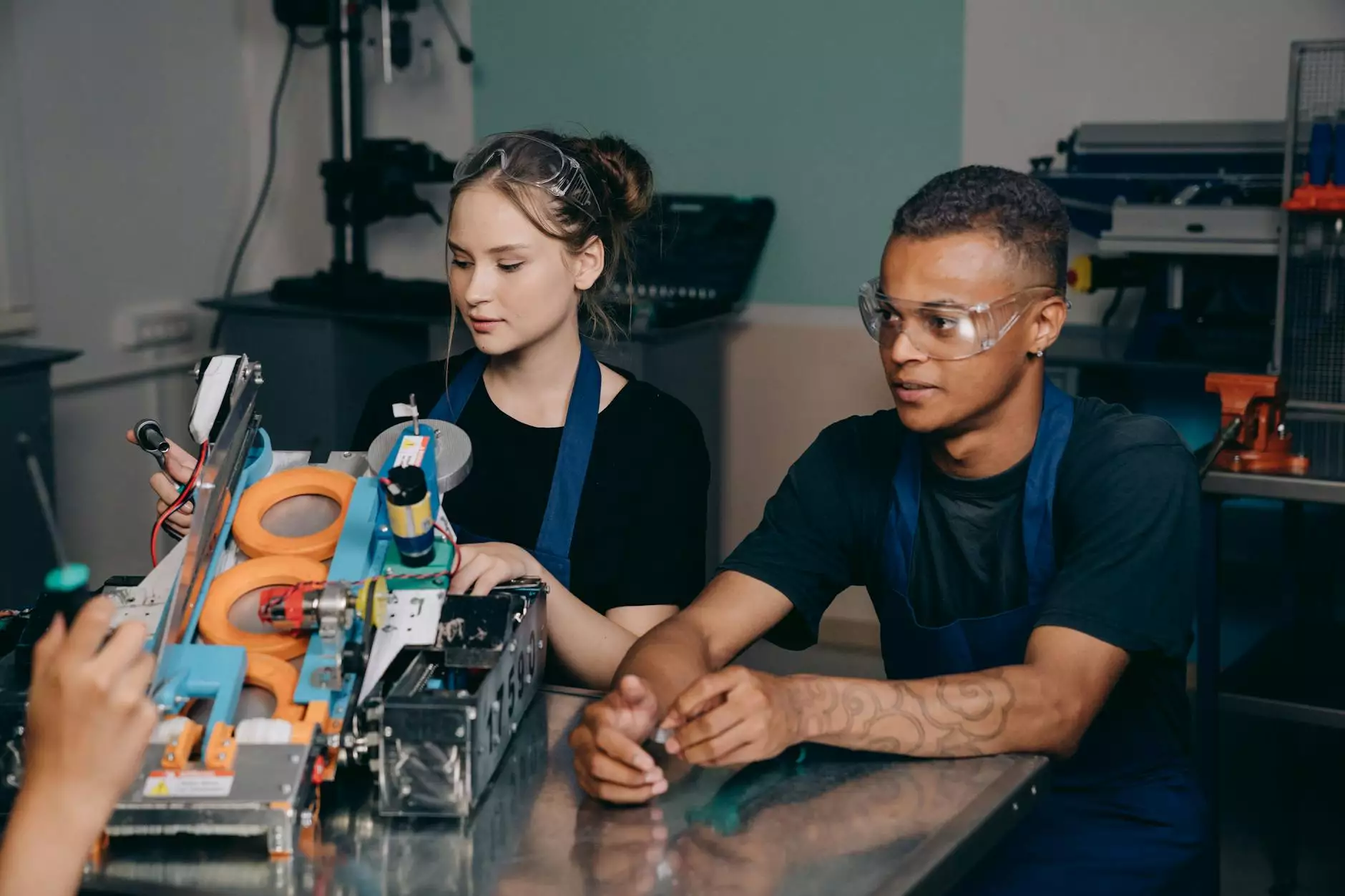
Die casting is a manufacturing process that involves forcing molten metal into a mold cavity under high pressure. Manufacturers worldwide have embraced this technique for its efficiency, precision, and ability to produce complex geometries. As we delve deeper into the realm of die casting parts manufacturers, we will uncover the significance, applications, and advantages of this remarkable process.
The Die Casting Process: An Overview
The die casting process can be summarized through several key stages:
- Preparation: The process begins with the preparation of the die, which is typically made from hardened steel or other durable materials. The die consists of two halves: the stationary half and the moving half.
- Melting: The metal, commonly aluminum, zinc, or magnesium, is heated in a furnace until it reaches a molten state.
- Injection: Once melted, the molten metal is injected into the die cavity under high pressure.
- Cooling: After the metal has been injected, it is allowed to cool and solidify within the mold.
- Ejection: Once cooled, the die halves are separated, and the solidified part is ejected from the mold.
- Finishing: Finally, any necessary finishing processes, such as trimming or surface finishing, are performed to enhance the product's quality.
Benefits of Die Casting for Manufacturers
Die casting offers several advantages that make it a preferred choice among manufacturers:
- High Efficiency: The die casting process is highly efficient, allowing for rapid production rates. This efficiency translates to lower manufacturing costs and faster project turnaround times.
- Complex Designs: Manufacturers can create intricate and complex designs that are often impossible to achieve through other methods.
- Precision and Consistency: Die casting produces parts with exceptional dimensional accuracy and uniformity, ensuring that each component meets stringent quality standards.
- Reduced Waste: The die casting process minimizes material waste compared to traditional manufacturing techniques, making it a more environmentally friendly option.
- Variety of Materials: Die casting can be performed using a variety of metallic alloys, enabling manufacturers to select the material that best suits their application needs.
Industries that Benefit from Die Casting
The versatility of die casting means it is employed across a range of industries, including:
- Aerospace: Lightweight and durable components are critical for aircraft and spacecraft, making die casting an ideal choice.
- Automotive: Die casting is extensively used for producing engine parts, transmission housings, and decorative elements.
- Electronics: The electronics industry leverages die casting for heat sinks, housings, and various mechanical components.
- Consumer Goods: From appliances to tools, die casting helps create reliable and appealing products.
- Medical Devices: Precision and reliability are essential in medical devices, where die casting ensures adherence to strict safety and quality standards.
How to Choose the Right Die Casting Parts Manufacturer
Choosing the right die casting parts manufacturer is crucial for achieving the desired quality and performance in your projects. Here are some key factors to consider:
Experience and Expertise
Look for manufacturers with extensive industry experience and expertise in die casting. Their knowledge can help navigate the intricacies of producing high-quality parts.
Equipment and Technology
Ensure the manufacturer is equipped with modern, reliable machinery and technology crucial for precision die casting. Advanced equipment can enhance accuracy and efficiency.
Quality Assurance
Inquire about the manufacturer’s quality control processes. A manufacturer committed to quality assurance will have rigorous testing methods in place to ensure that the final products meet industry standards.
Material Selection
The versatility of die casting allows for different materials. Check if the manufacturer can work with the specific materials that suit your application, whether aluminum, zinc, or magnesium.
Customer Service
Look for a manufacturer who prioritizes customer service. Open communication, responsiveness, and a collaborative approach can greatly enhance your overall experience.
The Future of Die Casting
As technology advances, die casting is poised for significant developments. Innovations such as:
- 3D Printing: Integrating 3D printing for mold creation can streamline the process and reduce lead times.
- Improved Alloys: Ongoing research into new alloys enhances the performance characteristics of die-cast products.
- Automation: Further automation in the die casting process can improve efficiency and reduce labor costs.
- Environmental Considerations: Manufacturers are increasingly adopting environmentally friendly practices to reduce their carbon footprint.
Conclusion
In summary, die casting parts manufacturers play a pivotal role in various industries, offering significant advantages in terms of efficiency, precision, and waste reduction. By understanding the process, benefits, and considerations for selecting a manufacturer, businesses can make informed decisions that contribute to their success. As we look to the future, the potential for innovation within the die casting industry is vast, promising continued improvement and expansion of its applications.
Explore More at DeepMould.net
To learn more about die casting, visit DeepMould.net. Our expertise in metal fabricators ensures that we are at the forefront of industry standards, delivering exceptional quality and service to our clients.